This website uses cookies so that we can provide you with the best user experience possible. Cookie information is stored in your browser and performs functions such as recognising you when you return to our website and helping our team to understand which sections of the website you find most interesting and useful.
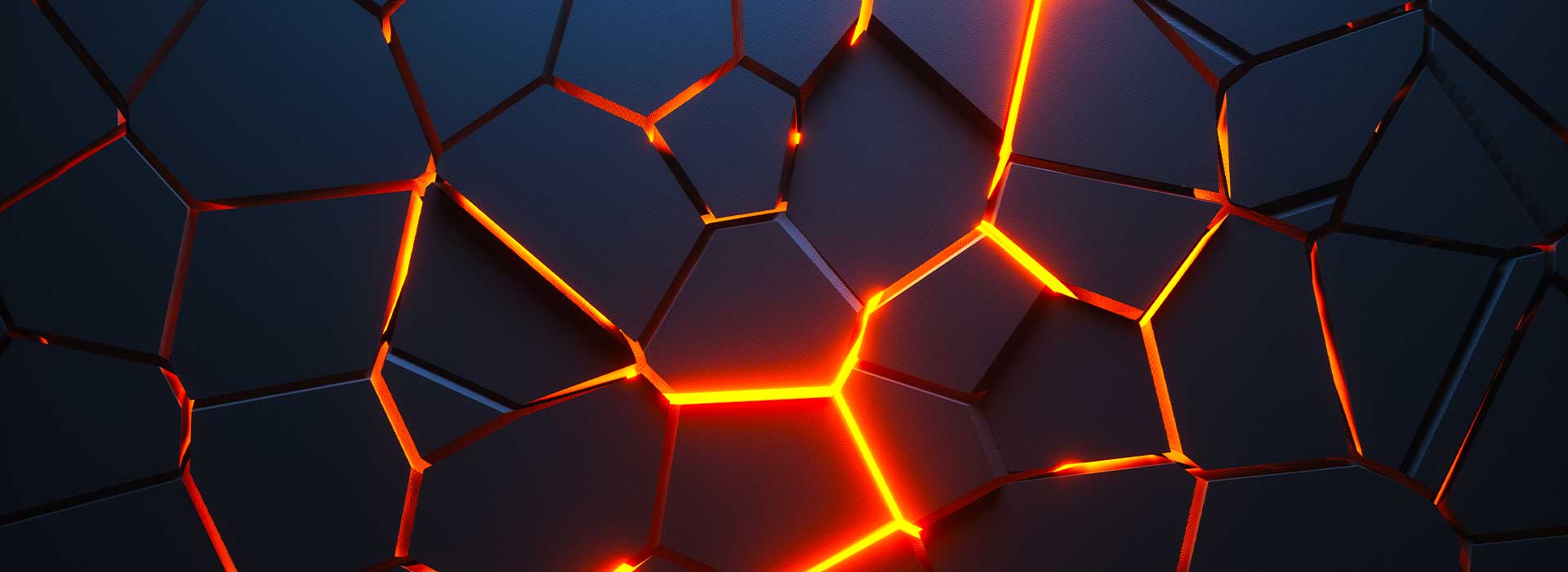
Thermomechanics
Thermomechanical simulation is a powerful tool for understanding and predicting the behavior of materials and systems subjected to thermal and mechanical loads. It offers significant advantages in terms of optimized design, failure prevention, reduced development time and costs, and understanding of physical phenomena. This makes it possible to identify critical zones at actual operating temperatures, optimize operation or maintenance, better target physical tests, substitute materials, redesign and limit post-realization modifications. The solution will be built up through iterations that numerically reproduce the product’s thermomechanical behavior.
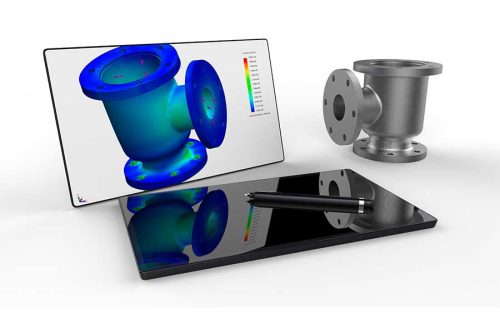
Thermomechanical simulation can be used for the entire product life cycle, including :
Our teams are ready to provide you with invaluable technical support for your cooling system design projects or to anticipate material reactions to sudden temperature variations. With their solid expertise in mechanical behavior laws and material properties, including complex media, our specialized engineers will guide you with confidence. Our commitment encompasses :
- Evaluate the performance of your products under their operating conditions and optimize their performance by substituting materials, adding coatings or improving geometry (e.g. optimizing cooling channels).
- The coupling of thermal analysis results with a mechanical study (unidirectional or bidirectional), or even with a fluid-structure interaction (FSI) study or CFD analysis.
- Consideration of all types of heat transfer: conduction, natural or forced convection, radiation, but also phenomena such as phase changes or energy deposits.
The choice of tools is systematically made in consultation with your teams, so that they can reinternalize the models if they so wish. The main tools used are :
for its ability to perform advanced thermomechanical analyses. It offers a wide range of functions for modeling and solving heat transfer, strain and stress problems.
To ensure you get the right answers, our teams provide active support, guiding you through the entire process: from identifying your initial needs to implementation, ensuring a solution that’s right for you at every stage of your project.
- Validation of the numerical model representative of the real system you wish to study. By taking into account the appropriate thermal and mechanical properties of the material, as well as the interactions between the different parts of the system, and even by choosing acceptable analogies.
- Definition of boundary conditions such as temperature conditions, applied stresses, external forces, etc.
- Creating the discretized model: Proper meshing is essential to obtain accurate results, while keeping model sizes and calculation times easily manageable.
- Material data correlation, experimental validation, supervision of physical tests and numerical modeling.
- Analysis and interpretation of results with the project team to validate options or define additional iterations to be considered.
Examples of realizations :
Thermomechanical simulation is essential in medtech, particularly for the development of orthopedic prostheses. For example, when designing a hip prosthesis, simulations can be used to assess the mechanical stresses and temperature changes to which the prosthesis is subjected during patient movement. These analyses help to optimize geometry, materials and manufacturing processes, ensuring the prosthesis’s durability, biological compatibility and long-term performance.