This website uses cookies so that we can provide you with the best user experience possible. Cookie information is stored in your browser and performs functions such as recognising you when you return to our website and helping our team to understand which sections of the website you find most interesting and useful.
Numerical simulation for watchmaking: between tradition and innovation
Swiss excellence in watchmaking and art mechanics is now inscribed on the Representative List of the Intangible Cultural Heritage of Humanity.
The Swiss watchmaking industry is a cutting-edge one, with many inventions and world firsts to its credit. It was founded in Geneva in the mid-16th century, and the city quickly gained a reputation for excellence in watchmaking.
It continues to promote the finest watchmaking expertise at world-renowned trade shows such as Watches and Wonders and EPHJ.
It’s only natural that DAES should follow in this tradition of excellence and offer its watchmaking engineering services: from the linear mechanical analysis of springs, to the CFD study of air flows in contact with pendular elements, via studies of hunting, shock, dynamic and vibratory analysis, our expert numerical calculation engineers support the R&D of watchmaking projects.
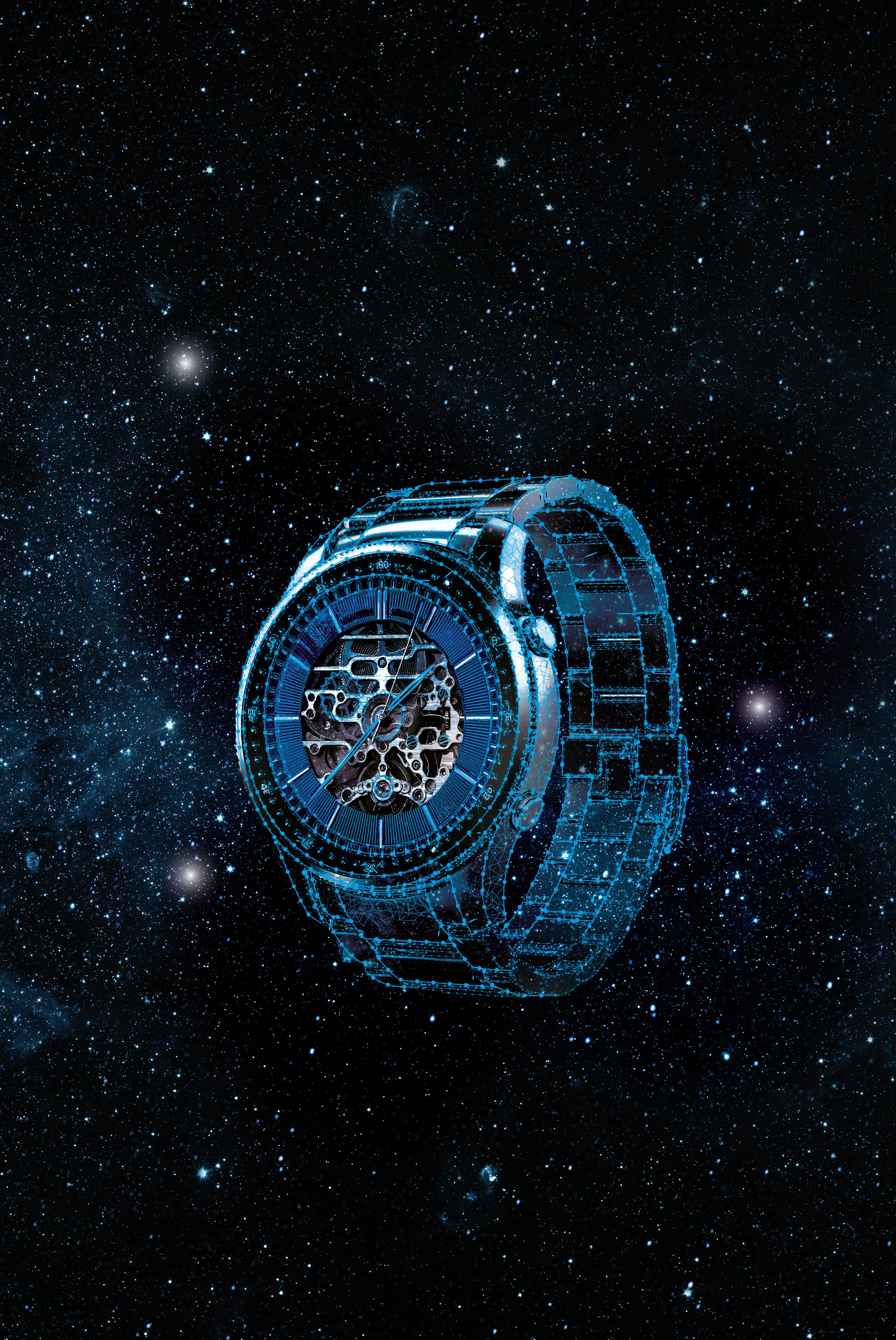
Watchmaking and its complications
The wristwatch is a constant reminder of the wearer’s most precious possession : time ! Choose who or what you’re going to spend it on, with a focus on quality, durability, precision and leaving a lasting impression.
Swiss watchmaking has maintained its position as world market leader for centuries. It is known and recognized for its dynamism and creativity, always capable of meeting new technological, economic and other challenges.
His many inventions and world firsts include the first water-resistant wristwatch, the world’s flattest wristwatch, the world’s smallest wristwatch, and many more…
Simulation techniques can be used to virtualize complications, systems and other miniaturized elements. They are an invaluable aid to the success of your R&D and design projects.
Here are just a few examples of the possibilities offered by digital simulation
DAES’ Technical Director is behind the deployment of computing capabilities in the watchmaking sector. He took part in the first major computing project and trained many engineers in the field. Today, we continue to work with watchmakers on cutting-edge calculation issues, while bringing digital simulation upstream in the design process. Thanks to simulation, ever more audacious projects can be envisaged without compromising on the final result. This makes the engineering process for these complex objects increasingly efficient, particularly from a quality and reliability point of view, avoiding sizing errors that will only be detected later during the test phases, or even later when the watch is on the customer’s arm.
finite element calculation
As with a car crash test, numerical simulation tools such as LS-DYNA or ABAQUS can be used to estimate the consequences of a watch falling from different heights. The drop can be studied for different components, such as the crystal, the case middle or the internal mechanism. It’s also easy to adapt materials to see how a failure can be resolved by choosing a stronger or more ductile material.
This type of calculation, dynamic analysis, can represent a falling watch (in which case different angles can be considered) or a sheep-pendulum test to NIHS standards. In all cases, the stresses in the various components can be checked, ensuring the integrity of the watch in the event of a fall.
A typical watchmaking test consists of checking the tensile and torsional strength of the bracelet and the watch, in particular the caseband and its connection to the bracelet. Modelling techniques similar to those used for the above-mentioned drop studies can then be used: dynamic analysis with LS-DYNA.
The complexity of these studies lies in the assembly’s large number of degrees of freedom. Each link in the bracelet is taken into account, adding degrees of freedom (DoF) that the software must process. What’s more, pins, pivots and every contact are taken into account and modeled, resulting in lengthy non-linear calculations. This type of calculation requires a great deal of know-how to obtain results in line with physical reality, while allowing models to converge numerically in a reasonable time.
At the heart of watchmaking engineering lie the complications. The aim is to create a purely mechanical mechanism that still uses the energy of the barrel spring, the motor of the watch, which can be recharged by the potential energy of gravity in the case of automatic winding. This stored energy is used to ensure the isochrony of the mechanism and to animate a dial for the days of the week, the months of the year, or day and night, depending on the complications in the system.
The dissipation of this stored energy must therefore be optimized. Thanks to the expertise of our engineers and state-of-the-art tools (such as LS-DYNA, ANSYS…), it is possible to model these mechanisms and predict their operation. This is the virtual laboratory of your extended enterprise! Evaluating actuating forces using rigid or flexible body calculations, the complete dynamics of complex mechanisms can be assessed, taking into account backlash and other geometric imperfections. Actuating forces can be calculated for rigid or flexible bodies, and the complete dynamics of complex mechanisms can be assessed.
Our numerical simulations don’t just give you a result, they give you an inside view of what your parts undergo during the different operating modes to which they are subjected.
We used to do a bit of calculation, a lot of testing and prototyping… today we can do multiple virtual prototypes and only one test.
It’s been said that watchmaking is Formula 1 in its smallest form! Yes, resistive forces caused by viscous friction have an impact on the movement of parts. That’s why it’s important to take them into account. In movement design, reducing friction is a constant quest. The air contained in watches causes viscous friction, which increases resistive forces and therefore influences the isochrony of the mechanism. CFD studies can be used to estimate the forces associated with this type of friction.
One of the keys to the know-how of DAES engineers lies in the use of advanced materials modeling. In fact, the behavior of a precious metal like gold and that of ceramics are completely different. These 2 examples are the simplest to deal with, as some materials often have far more complex behaviors, such as hyper-elastic joints. Their integration into simulations, the right choice of material model and the associated post-processing criteria are therefore crucial to obtaining the most relevant results.
The geometry of the crystal can have a significant influence on the view of the dial, and therefore on user comfort. Using dedicated calculations, the dial image perceived by the eye can be verified for different geometries and user positions.
We are now bathed in a man-made electromagnetic field. Depending on the materials chosen for the watch components, a remanent field may appear after the surrounding field has disappeared. However, a magnetic field causes stresses on the components that can affect the watch’s precision. A FE analysis can be set up to estimate this remanent field and the resulting stresses.
Watchmaking is a skilful balance between modernity and tradition. Customer typology is evolving, and for some years now it has been essential to provide answers on the origin of materials, the use of recyclable or recycled materials, vegetable leathers…
CSR is increasingly expressed “around the product” in terms of packaging, energy management in factories, sourcing of precious metals, offsetting carbon footprints, relations with suppliers, etc. In engineering, the use of digital simulations makes a major contribution to this commitment.
Applications on the move between sectors
Watchmaking applications naturally transfer to biomedical engineering to help the medtech industry develop and design innovative medical devices for curative, preventive or predictive medicine.