This website uses cookies so that we can provide you with the best user experience possible. Cookie information is stored in your browser and performs functions such as recognising you when you return to our website and helping our team to understand which sections of the website you find most interesting and useful.
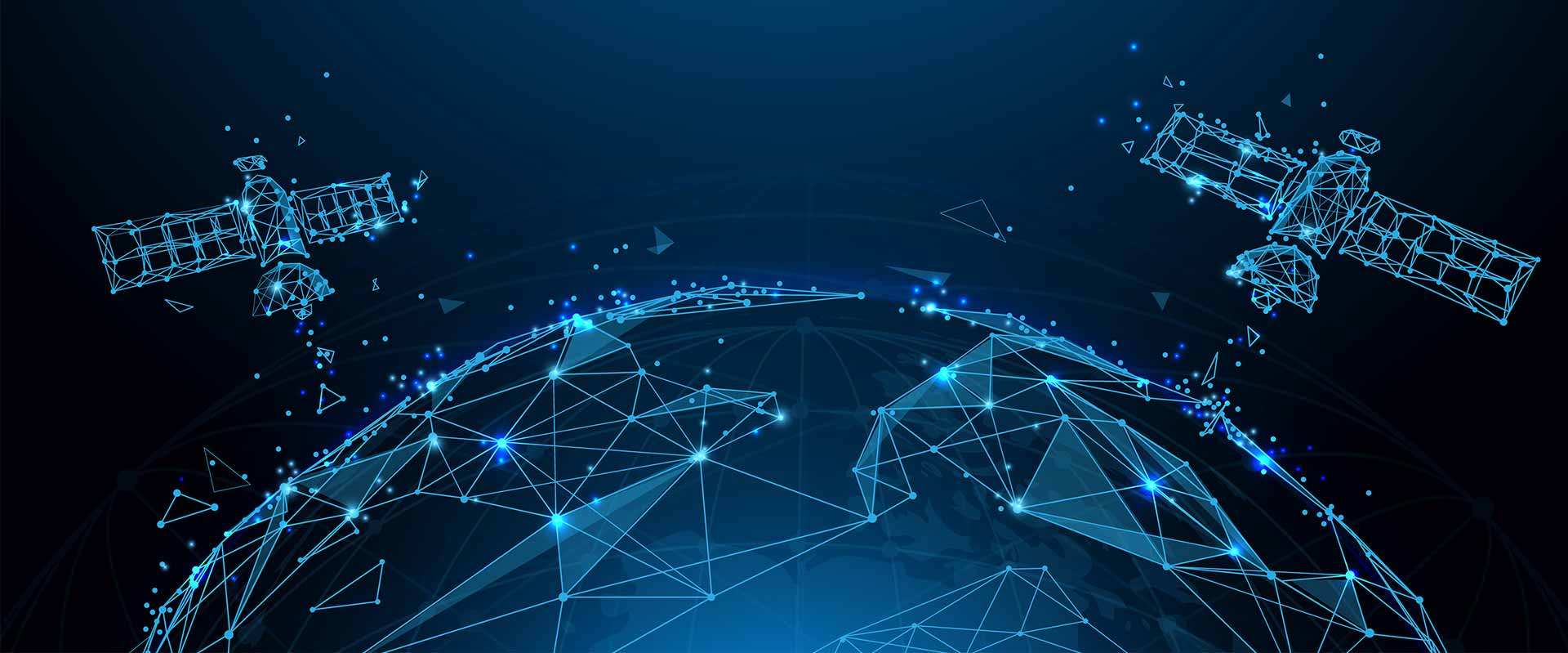
Aerospace: a sector where simulation is essential!
Aerospace encompasses aeronautics and astronautics, two distinct disciplines.
An aircraft is a device that moves through the atmosphere under its own power, the main types being airplanes, helicopters and drones.
An aircraft flies thanks to the flow of air around the wings, producing aerodynamic forces such as lift (perpendicular to the relative wind, upwards), generated by the pressure difference between the top and bottom of each wing; and drag (parallel to the relative wind, backwards). The technological challenge lies in obtaining the best weight/thrust ratio, which depends on the materials used (weight vs. strength) and the type of propulsion.
As in aeronautics, the limits concern weight and the external force required for take-off. Space missions involve extreme conditions: vibrations at lift-off, vacuum of space, radiation emitted by the Sun (from radio waves to gamma rays, highly energetic neutrons and charged particles – electrons, protons and others – which are also highly energetic), significant temperature differences due to the difference between the energy received from the Sun and the temperature of the cosmic microwave background (~3-4 K), terrestrial radiation belts (called Van Allen belts for the Earth) in which high-energy charged particles are trapped by our planet’s magnetic field, atmospheric re-entry of spacecraft on their return to Earth (intense friction between the craft and the atmosphere), etc…
DAES supports major players in this industry. From CFD calculations for airflow around an aircraft, to the structural design of composite parts and the application of safety standards, our experts can help you design your products.
The main objectives and challenges for aerospace include:
- Lower orbiting costs
- Developing high-performance propulsion systems that deliver high thrust
- Improving launcher structure
- Find technical solutions for reusing parts of the launcher
- Lower orbiting costs
- Lower spacecraft costs once in space
- Improving the efficiency of energy production systems
- Improving thermal and radiation protection systems
- Lower payload costs
- miniaturize instruments, reduce power consumption
Just a few examples of the possibilities offered by digital simulation!
Most areas of aerospace applications are covered by the expertise of DAES and its partners, making us your preferred partner.
- Space Launch Systems (SLS)
- Space launch vehicles (LV)
- Hard lashing systems
- Rocket propulsion
- Ion and plasma thrusters
- Spacecraft, satellites and a fleet of nanosatellites
- Space debris collection systems
Turbulent flow occurs around an aircraft. Locally, transition zones between laminar and turbulent flows may even appear.
CFD analyses allow us to take these effects into account and study their impact on the aircraft.
In some cases, the deformation created by fluid pressure must be taken into account. And vice versa, so does the change in shape of the part in contact with the airflow. This is known as coupled CFD analysis (or FSI Fluid-Structure Interaction).
Optical instruments on satellites must remain as stable as possible to remain accurate. Their design requires numerous numerical simulations, both using tools dedicated to optics such as ZEMAX, and to ensure the mechanical strength of these instruments. What’s needed is maximum stability and virtually zero thermal expansion. Carbon composite assemblies are often used for these purposes.
Space and non-space vehicles are subject to strong vibrations, particularly during take-off. Vibration analyses such as PSD or simplified structural static analyses can be used to estimate the resulting stresses. These calculations are essential for verifying the equipment’s ability to withstand the stresses to which it will be subjected, and for verifying its service life.
We all remember the impact of a piece of debris on the Air France concorde, Paris – New York. An impact on one of the vehicle’s external components during critical phases can have dramatic effects. Whether it’s an impact from a bird or space debris, explicit analyses (dynamic analyses) can be used to estimate the component’s resistance to such an impact, and thus to design countermeasures for these rare but unavoidable impacts.
Mass is a crucial issue in aerospace. Modern numerical simulations can be used to optimize the topology of a part subjected to defined stresses. Components are thus optimized while ensuring that their integrity is preserved. Obviously, material changes are often considered to perfect these optimization needs.
Whether it’s a rocket, an airplane or a helicopter, the components used in this equipment are subjected to extraordinary stresses. The stresses induced during the various phases (takeoff, landing, in-flight) can be estimated by transient or static structural analyses. The weight of these components is constantly optimized, while ensuring that their integrity is preserved. Obviously, material changes are often considered to perfect these optimization needs.
Expert in numerical simulation and much more!
Digital simulation engineers are often seen as experts, and can quickly become isolated. At DAES, our experts are more than just calculators: they are at the heart of your projects, driving innovation and product improvement.
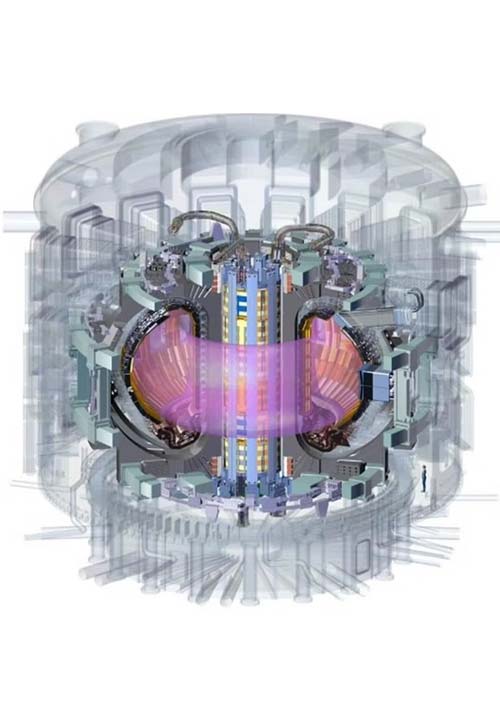
Euclid is anESA space mission whose aim is to understand why the expansion of the universe is accelerating, and to determine the nature of the energy source responsible for this acceleration. This energy, known as dark energy, and dark matter make up around 95% of the universe. Euclid will observe the evolution of the universe over the past 10 billion years, in an attempt to answer questions linked to the nature and properties of dark energy, dark matter and gravity: either dark matter consists of a new, previously unknown particle, or the fundamental law of gravity needs to be reassessed.
Euclid will be equipped with a 1.2 m-diameter silicon carbide telescope built to power 2 instruments, VIS and NISP, produced by the Euclid consortium: a high-quality panoramic visible imager (VIS), and an infrared spectrograph and photometer. The satellite will be launched in 2023 and will travel to Lagrange L2 for a 6-year mission.
As part of their previous activities at the Laboratoire d’Astrophysique de Marseille (LAM) of the CNRS, DAES collaborators were involved in the system engineering, optical design and testing of the NISP instrument developed under the direction of the LAM with the CNES.
- Definition of interfaces and technical specifications for partners in charge of manufacturing certain instrument components
- Validation of quality approach with industrial partners in charge of manufacturing optical components (application of space standards and definition of acceptance criteria).
- Definition of validation and qualification tests for optical components (thermal cycling and vibration)
- Supervision and development of mechanical assembly / integration / testing activities
- Design of Mechanical Ground System Equipment for assembly and integration of the NISP instrument
Design of facilities for NISP instrument validation and qualification tests (thermal cycling and vibration)
FIREBall -2 (Faint Intergalactic Medium Redshifted Emission Balloon) is a Franco-American scientific project launched in September 2018, whose aim is to detect faint emissions from the hot intergalactic medium. FIREBall carries out its measurements at an altitude of 40 km, with the instruments installed in a gondola mounted under a stratospheric balloon. FIREBall comprises a 1 m telescope and a spectrograph operating in the ultraviolet (200 nm wavelength): the FIREBall project is piloted by CALTECH, with flights provided by NASA, CNES supplying the gondola and LAM the spectrograph.
As part of his previous activities with the Marseille Astrophysics Laboratory (LAM) of the CNRS, the DAES collaborator was involved in the design, alignment and optical performance evaluation of the spectrograph from its conception to the flight campaign, as well as in the definition of a coupled instrumental model (Raytracing + Python) to simulate the instrument’s performance.
The PFS SuMIRe project (Prime Focus Spectrograph Subaru Measurement of Images and Redshifts) is an international project (USA, Japan, Brazil, France) aimed at answering fundamental questions about the creation of the universe. Scientists recently discovered that only 4% of the universe’s composition was known, the remaining 96% being made up of “dark matter”, which has never been detected directly, and “dark energy”, which accelerates the expansion of the universe. The PFS spectrograph, once installed on the 8.2-meter Subaru telescope at Mauna Kea (Hawaii), will be used for galaxy surveys, galactic archaeology and galaxy evolution studies. PFS will simultaneously spectroscope 2,400 targets using the Subaru telescope’s wide field of view and a spectrographic system consisting of four identical spectrographic modules (each powered by 600 fibers). Each spectrograph can simultaneously take measurements in the blue, red and near-infrared wavelengths. Each of the spectrograph’s four modules is assembled, integrated, tested and validated at LAM before being shipped to minimize integration and testing activities at the summit of Mauna Kea (4207 meters above sea level). As part of her previous activities at the Laboratoire d’Astrophysique de Marseille (LAM) of the CNRS, the DAES collaborator was involved in the optical design of the PFS spectrograph, in particular carrying out part of the optical calculation studies associated with the spectrograph (design, optical performance, tolerancing, stray light).