This website uses cookies so that we can provide you with the best user experience possible. Cookie information is stored in your browser and performs functions such as recognising you when you return to our website and helping our team to understand which sections of the website you find most interesting and useful.
Mechanical simulation
Mechanical simulation enables us to innovate more effectively, because it enables us to test and analyze a wide range of product configurations and designs virtually, without having to build costly and time-consuming physical prototypes.
Thanks to mechanical simulation, engineers can quickly test different combinations of materials, shapes and configurations to optimize product performance, while minimizing the risk of failure and high costs. Simulations can also help identify critical stress or strain zones, as well as determine the modifications needed to strengthen or improve the structure’s design.
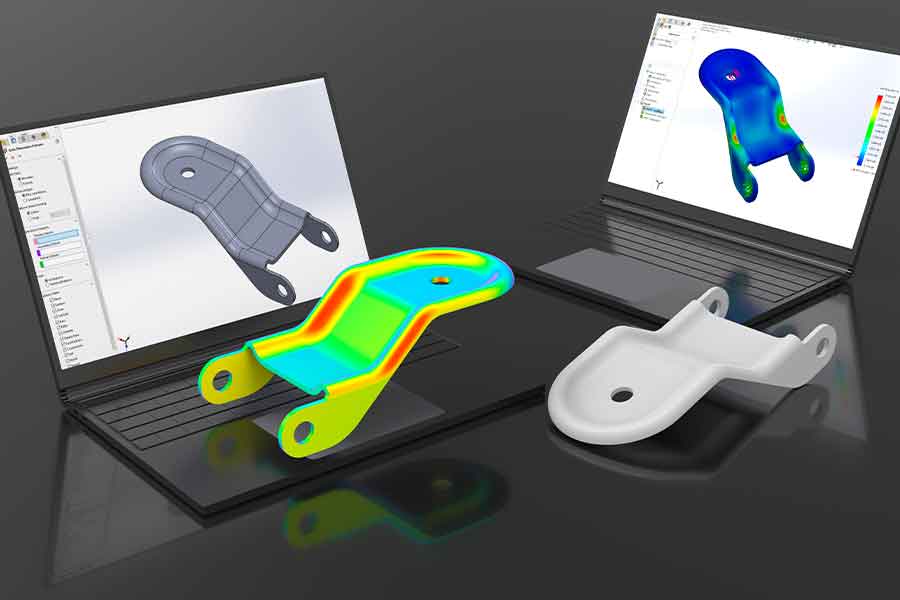
In addition, mechanical simulation enables new product concepts to be explored more effectively, which can lead to faster, more creative innovation. Engineers can test new ideas and explore bolder designs, quickly understanding how these new configurations might behave under real-life conditions.
Finally, mechanical simulation also enables us to better understand the performance and limitations of existing products. By identifying these limitations, engineers can work to optimize the design to improve performance and quality, while meeting customer needs more efficiently.
In short, mechanical simulation offers many advantages for innovating faster, more efficiently and more creatively, while minimizing the risks and costs associated with the design and development of new products.
There are several types of mechanical simulation that can be performed. Here are a few examples:
To perform a good mechanical simulation, it’s important to follow a methodical and rigorous process. Here are the key steps to follow:
- Define the problem: it’s essential to have a clear understanding of the problem you’re trying to solve and the objectives of the simulation. What is the structure or system of interest? What loads, stresses or forces are applied? What results are you looking to achieve? What type of analysis is required?
- Collect data: it’s important to collect all the data needed to model the system correctly. This can include material properties, structure dimensions, supports and applied loads, as well as environmental conditions.
- Create the model: using mechanical simulation software, you need to create a detailed model of the structure or system you wish to simulate. The model must include all relevant details, such as dimensions, materials and applied loads.
- Define load conditions and supports: you need to define the load conditions and supports that apply to the structure or system. These conditions may include static or dynamic loads, moments, pressures, vibration spectra, and so on.
- Run simulation: once the model and load conditions have been defined, you can run the simulation. You need to make sure you use the right numerical methods to solve the simulation equations and get accurate results.
- Analyze results: once the simulation is complete, you need to analyze the results and compare them with the simulation objectives. You need to identify critical areas, stresses, strains and other relevant parameters to determine whether the model meets requirements and specifications. Validating the numerical model (mesh quality, for example) is part of analyzing the results.
Readjust the model and repeat: if the results do not meet the simulation objectives, or if the model is not validated, you need to readjust the model and repeat the previous steps until you obtain satisfactory results.
In a mechanical simulation, we look at several parameters to assess the performance of a structure or system. The main parameters are :
In short, good mechanical simulation involves a clear understanding of the problem to be solved, accurate data collection, detailed model creation, the use of the right numerical methods, rigorous analysis of the results and any necessary adjustments to obtain accurate and relevant results.
Many software tools are available for mechanical simulation. The appropriate tools depend on the type of simulation you wish to perform and the complexity of the structure or system you wish to model. Here are a few examples of mechanical simulation tools:
1. ANSYS :
ANSYS is one of the most popular software packages for mechanical simulation. It offers a wide range of functionalities, including stress analysis, fatigue analysis, dynamic analysis, thermal analysis, fracture simulation and more. These phenomena can be coupled in a multiphysics analysis.
2. Abaqus :
Abaqus is another popular mechanical simulation software. It offers similar functionalities to ANSYS, including stress analysis, fatigue analysis, dynamic analysis, thermal analysis, fracture simulation and more. These phenomena can be coupled in a multiphysics analysis.
3. COMSOL Multiphysics :
COMSOL Multiphysics is a numerical simulation software package for simulating various types of physical phenomena, such as solid mechanics, thermics, electromagnetism, acoustics and more.
4. MSC Nastran :
MSC Nastran is a mechanical simulation software package for stress analysis, structural dynamics analysis, fatigue analysis and more.