This website uses cookies so that we can provide you with the best user experience possible. Cookie information is stored in your browser and performs functions such as recognising you when you return to our website and helping our team to understand which sections of the website you find most interesting and useful.
Numerical simulation to optimize energy performance and control costs!
It’s a global challenge: energy transition, global warming, carbon footprint, sovereignty, cost control… every stage in the value chain is concerned with energy management. Our engineers work on behalf of energy producers and their equipment manufacturers, as well as on international collaborative R&D projects to identify new technologies (electrolysers, thermo-acoustics, etc.).
Optimizing equipment design
Any energy-related project involves a chain of players and subcontractors who own a defined part of the system that will be interfaced with others, and is impacted both upstream and downstream by more global engineering decisions. Simulations enable companies to design and optimize mechanical equipment used in the production, transmission and distribution of energy, such as turbines, pumps, valves, pipes, etc., and to anticipate both commissioning and operation. This means better performance and greater energy efficiency.
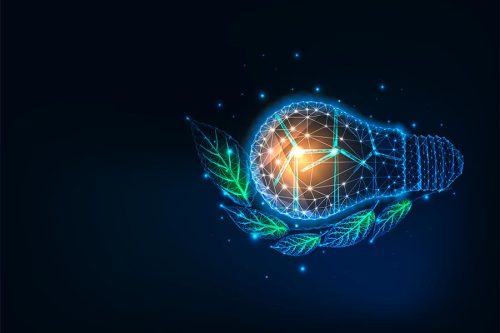
Failure analysis
The reliability of safety components is critical. Industrial risk management involves the safe operation of equipment. What’s more, given the high cost of downtime, it’s essential to anticipate the risk of failure, so as to be able to draw up robust maintenance plans. Simulations enable potential failures of mechanical equipment to be simulated and analyzed, so that areas at risk can be identified and measures taken to reduce them.
Reduce costs and lead times
Simulations help to reduce costs and development times by testing and optimizing equipment and processes virtually, before they are physically implemented, or by exploring virtual tests that cannot be reproduced physically. Our teams work directly with our customers’ innovation boards and R&D teams to simulate each key stage of the project.
Some examples of numerical simulation for energy
Innovating for the future: digital simulation drives innovation!
Numerical simulation to optimize energy performance and control costs!
Cleantech (or Clean Technology) refers to all clean or green technologies that aim to reduce the environmental impact of human activities while improving efficiency and productivity.
Cleantech technologies cover a wide range of fields, including renewable energy (solar, wind, hydro, geothermal), waste management, water treatment, sustainable mobility, eco-friendly materials, intelligent buildings, clean energy production and distribution, and more.
The main aim of Cleantech is to provide sustainable solutions that reduce greenhouse gas emissions and preserve natural resources, while creating new economic opportunities for businesses and improving people’s quality of life.
It’s only natural that DAES should support you in these projects.
Product design and optimization
Simulation of materials and performance
Risk and sustainability analysis
Process planning and optimization
Some examples of digital simulation for Cleantec
Simulation enables us to anticipate the environmental impact of a wind farm. When wind passes through such a field, the flow structure is altered, which can have an impact on the surrounding flora. A CFD calculation can be used to anticipate changes in this flow.
Similarly, by analyzing the resulting pressures, the acoustics of these machines can be estimated and their impact on local residents assessed.