This website uses cookies so that we can provide you with the best user experience possible. Cookie information is stored in your browser and performs functions such as recognising you when you return to our website and helping our team to understand which sections of the website you find most interesting and useful.
Design Thinking Engineering
Design Thinking Engineering is an approach to product or system design that combines the principles of design thinking and engineering. The aim is to develop products and systems that meet users’ needs through digital prototyping, by digitizing as many stages of the engineering and design process as possible.
More and more often, projects involve international, delocalized or parallel hierarchical teams who have to succeed together. They don’t have the same culture, nor the same history, and they don’t share the same working methodologies.
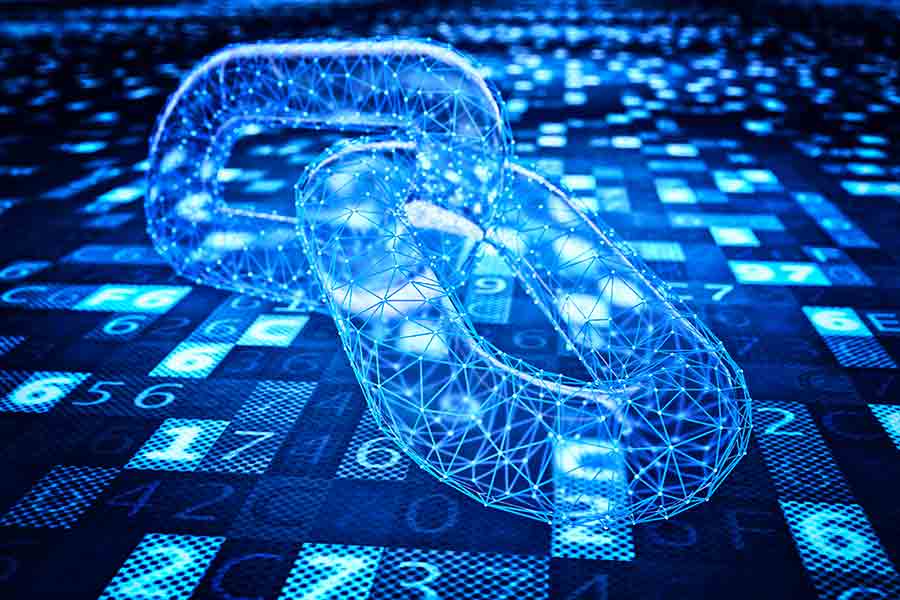
These teams have to work with their own tools and those of others to reduce development time and secure the prototyping, pre-production and production phases.
These tools don’t always talk to each other, and the sometimes heterogeneous data is rarely usable without reprocessing. Teams need to redouble their vigilance and agility.
They can also choose to be accompanied by our teams. DAES to support data analysis, communicate their toolboxes and rethink their Design Thinking Engineering: what input/output for simulations, what format, what flexibility is possible, how to limit inconsistencies while preserving a good level of relationships between project players?
Our specialized engineers support project teams in mapping out the engineering process, analyzing the tools used, benchmarking market solutions, drawing up functional specifications, and developing scripts or apps to transfer information throughout the development cycle.
An extension of systems thinking in engineering, the Design Thinking Engineering approach will also enable teams to explore possible evolutions of their products or systems very easily, by rapidly and digitally testing new concepts and integrating stakeholders more fully into the digital environment.
More than just digitizing design processes, it’s about intelligence in design modes, to reduce Time 2 Market while improving products!
Here are a few reasons why Design Thinking Engineering can be useful:
The simulation engineer plays an important role in the Design Thinking Engineering process, helping to evaluate the performance of products or systems throughout their life cycle.
Because they are able to propose virtual test developments, our engineers will also, where possible, work on their automation and on the creation of codes to create gateways between the different tools.
This makes it possible to :
- simplify the simulation process by enabling the exchange of information between different applications and simulation platforms.
- improve simulation engineer productivity by reducing the time and effort needed to transfer data between different tools.
- Securing the product design and launch chain
The Design Thinking Engineering process enables rapid evaluation of the design stages, and quickly “hunts down false ideas” by facilitating the transmission of data from one stage to the next.
For example, simulation engineers can create gateways to transfer data between computer-aided design (CAD) software and simulation tools to create complete digital models. This reduces the time needed to create simulation models, minimizes data transfer errors, and automates production to enable real-time monitoring and updating of simulation models.
In addition, gateways can be used to integrate data from different sources, such as material databases and design standards, to improve the accuracy of simulation models. Simulation engineers can also use gateways to automate repetitive tasks and manage complex data.