This website uses cookies so that we can provide you with the best user experience possible. Cookie information is stored in your browser and performs functions such as recognising you when you return to our website and helping our team to understand which sections of the website you find most interesting and useful.
Ingegneria del pensiero progettuale
Il Design Thinking Engineering è un approccio alla progettazione di prodotti o sistemi che combina i principi del design thinking e dell’ingegneria. L’obiettivo è sviluppare prodotti e sistemi che soddisfino le esigenze degli utenti utilizzando prototipi digitali, digitalizzando il maggior numero possibile di fasi del processo di progettazione e design.
Sempre più spesso, i progetti coinvolgono team internazionali, delocalizzati o con gerarchie parallele, che devono avere successo insieme. Non hanno la stessa cultura, lo stesso background o gli stessi metodi di lavoro.
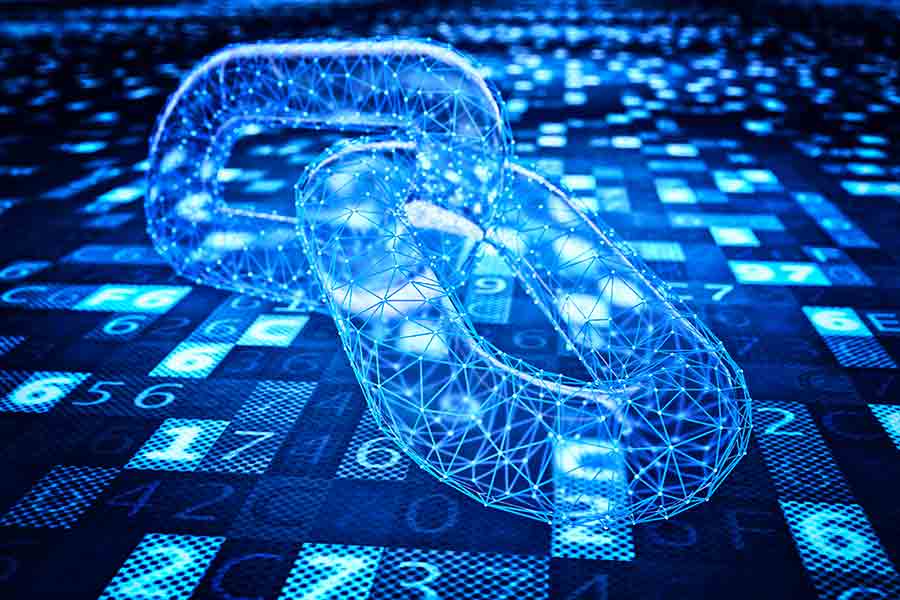
Questi team devono lavorare con strumenti propri e altrui per ridurre i tempi di sviluppo e garantire le fasi di prototipazione, pre-produzione e produzione.
Questi strumenti non sempre si parlano tra loro e i dati, a volte eterogenei, sono raramente utilizzabili senza una rielaborazione. I team devono essere ancora più vigili e agili.
Possono anche scegliere di essere supportati dai team DAES per supportare l’analisi dei dati, comunicare le loro cassette degli attrezzi e ripensare il loro Design Thinking Engineering: quali input/output per le simulazioni, quale formato, quale flessibilità è possibile, come limitare le incoerenze preservando un buon livello di relazioni tra gli attori del progetto?
I nostri ingegneri specializzati supportano i team di progetto nella mappatura del processo di progettazione, nell’analisi degli strumenti utilizzati, nel benchmarking delle soluzioni di mercato, nella stesura delle specifiche funzionali e nello sviluppo di script o app per trasferire le informazioni durante il ciclo di sviluppo.
Estensione del pensiero sistemico nell’ingegneria, l’approccio Design Thinking Engineering renderà molto semplice per i team esplorare possibili modifiche ai loro prodotti o sistemi, testando rapidamente e digitalmente nuovi concetti e coinvolgendo maggiormente le parti interessate nell’ambiente digitale.
Più che di digitalizzazione dei processi di progettazione, si tratta di intelligenza nei metodi di progettazione, per ridurre il Time 2 Market e migliorare i prodotti!
Ecco alcuni motivi per cui il Design Thinking Engineering può essere utile:
L’ingegnere simulatore svolge un ruolo importante nel processo di Design Thinking Engineering, aiutando a valutare le prestazioni di prodotti o sistemi durante il loro ciclo di vita.
Poiché sono in grado di offrire lo sviluppo di test virtuali, i nostri ingegneri si occuperanno anche, ove possibile, di automatizzarli e di creare codice per creare ponti tra i diversi strumenti.
In questo modo è possibile :
- semplificare il processo di simulazione consentendo lo scambio di informazioni tra diverse applicazioni e piattaforme di simulazione.
- Migliorate la produttività dei tecnici di simulazione riducendo il tempo e l’impegno necessari per trasferire i dati tra strumenti diversi.
- Garantire la catena di progettazione e lancio del prodotto
Il processo di Design Thinking Engineering consente una rapida valutazione delle fasi di progettazione e la “caccia veloce alle false buone idee”, facilitando la trasmissione dei dati da una fase all’altra.
Ad esempio, i tecnici della simulazione possono creare gateway per trasferire i dati tra il software di progettazione assistita da computer (CAD) e gli strumenti di simulazione per creare modelli digitali completi. Questo riduce i tempi di creazione dei modelli di simulazione, minimizza gli errori di trasferimento dei dati, automatizza la produzione per consentire il monitoraggio e gli aggiornamenti in tempo reale dei modelli di simulazione.
Inoltre, i gateway possono essere utilizzati per integrare i dati provenienti da fonti diverse, come i database dei materiali e gli standard di progettazione, per migliorare l’accuratezza dei modelli di simulazione. I tecnici della simulazione possono anche utilizzare i gateway per automatizzare le attività ripetitive e gestire dati complessi.